Hello everyone, Vincent here from our metal fabrication workshop. Today, I want to talk about something that might seem a bit technical, but is absolutely crucial in the world of custom metal parts — tolerances. If you’ve ever wondered why precision is such a big deal in metal fabrication, or why we keep going on about tolerances, this is the post for you.
What Are Tolerances?
In the simplest terms, tolerances are the allowable limits of variation in the dimensions of a metal part. They indicate how much a part can deviate from the specified dimensions while still being considered acceptable. Precision, therefore, is how closely the part meets its specified measurements.
Why Do Tolerances Matter?
Imagine you’re designing a custom component that needs to fit perfectly into a larger assembly, perhaps in aerospace or automotive manufacturing. If this component is too big or too small, even by a small fraction, it might not fit at all, or it could cause the assembly to fail. That’s where tolerances come into play.
The Impact of Precise Tolerances
1. Ensuring Interchangeability
With tight tolerances, parts can be interchangeable. This means they can be replaced with other similar parts without any issues with fitment. This is crucial in high-volume manufacturing where consistency and uniformity are key.
2. Maintaining Functionality
Many mechanical systems rely on components fitting together with precise clearances to function correctly. Whether it’s gears in a gearbox or pistons in an engine, the tolerances determine the efficiency and performance of the system.
3. Supporting Safety
In many industries, especially where safety is paramount like in aerospace and automotive, tolerances are critical. A small error could potentially lead to catastrophic failures. Precise tolerances help prevent these issues and ensure the safety of the end-users.
4. Reducing Costs
While tighter tolerances often increase the manufacturing cost due to more stringent quality control and slower production speeds, they can actually save money in the long run. How? By reducing waste and minimizing the need for rework or adjustments during assembly.
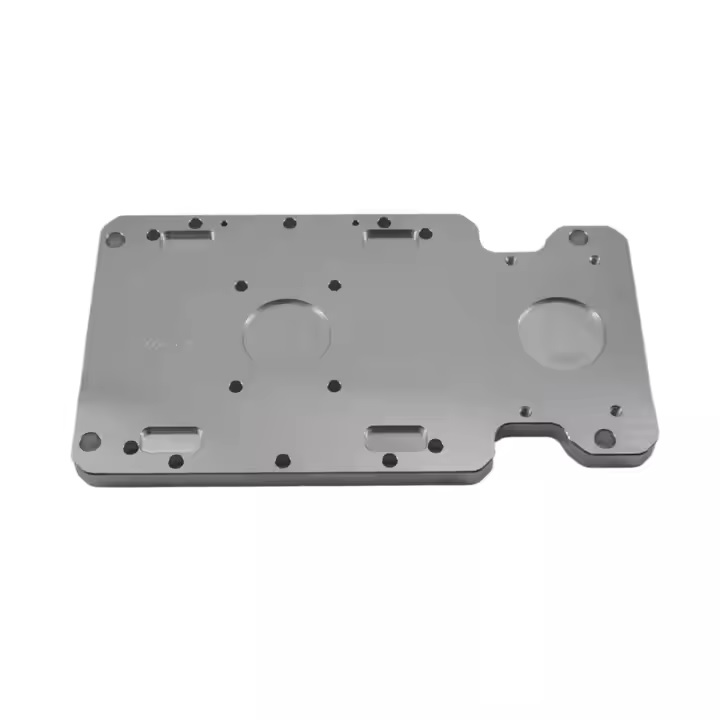
Balancing Tolerance, Cost, and Practicality
While it might seem ideal to aim for the tightest tolerances possible, it’s not always practical or cost-effective. Here’s how we balance these factors:
1. Material Choice
Different materials behave differently under the same machining processes. Understanding the properties of the material can help in setting realistic tolerances.
2. Manufacturing Techniques
Some manufacturing methods are more precise than others. For instance, CNC machining can achieve much tighter tolerances than casting. Choosing the right process for the job is crucial.
3. Part Application
The intended use of the part often dictates how tight the tolerances need to be. High-stress applications might require more precision, whereas decorative items might allow for more leeway.
4. Cost Constraints
Tighter tolerances require more time and skill to achieve, which can drive up costs. We work with our clients to find the right balance between precision and budget.
Conclusion
In the world of custom metal fabrication, precision isn’t just about meticulousness or perfectionism—it’s a fundamental aspect that affects the functionality, safety, and overall success of the product. At our shop, we take pride in our ability to meet precise specifications and help our clients understand the importance of tolerances in their projects.
If you’ve got a project in mind or need advice on how to set tolerances for your next component, feel free to drop by or give us a call. We’re here to ensure your parts aren’t just made, but made right.
Here’s to building things that fit perfectly, every time.